B3500 Convection Reflow Oven
5-Zone Lead-Free Convection Reflow System with Combination Edge-Pin/Mesh-Belt
Conveyor and Windows-Based OS!
Part of our popular B-Series of premium-quality, small-footprint reflow systems, the B3500
includes 5 full zones of hot-air convection heating, each with independent upper and lower
temperature controls, a combination adjustable edge-pin/stainless steel mesh belt conveyor,
three thermocouple inputs, and a computer controller with a user-friendly Windows-based
operating system for precision temperature profiling.
◎ Affordably-priced, 5-zone "lead-free" model suits a full range of production requirements
◎ High-mass heat sources and efficient flow design allow full, forced convection reflow in a footprint 20%-30% shorter than comparable systems
◎ Independent upper and lower PID temperature controls for each heat zone and three thermocouple inputs for accurate "lead-free" temperature profiling
◎ Combination stainless steel mesh belt and adjustable edge-pin-type conveyor handles
◎ PCBs up to 450 mm wide; 550 mm on mesh belt
◎ Easy-to-use Windows-based user interface with advanced temperature profiling and thermal management functions
◎ Timed automatic startup and shutdown modes for power management and energy
◎ conservation
◎ Includes industrial PC, LCD flat-screen monitor
◎ UPS battery backup to ensure product protection in the event of power outage (Optional)
◎ CE certified
◎ Small footprint - only 3m length
General:
Tin Lead (SnPb) Compatible
Double-Sided Board Processing
CE Compliance
SMEMA Compatible (Optional)
Board Handling:
Heated Board Width: 570mm
Mesh Belt Conveyor (Standard)
Mesh Belt Width: 570mm
Chain-Driven Pin Conveyor (Standard)
Pin Conveyor Max. Width: 450mm
Pin Conveyor Min. Width: 50mm
Auto Adjust Pin Conveyor (Optional)
Powered Center Support (Optional)
Automatic Chain Lubrication
Conveyor Speed: 400-1800mm/min
Conveyor Height: 900mm ±20mm
Conveyor Direction: Left to Right
Component Max. Height: 30mm upper, 25mm lower
Heating:
Forced Hot Air Convection
Number of Independently Controlled : 10 total
Heating Zones: 5 upper, 5 lower
Total Heated Length: 1910 mm
Number of Oven Convection Motors: 10 / Power: 120W x 10
Delta T: ±2° C
Temperature Controls:
PID (Proportional-Integral-Differential)
Temperature Control Accuracy :±1° C
PCB Temperature Tolerance :±2° C
Temperature Range: Ambient -300° C
Ramping Time (from cold start): < 15 min
Profiling / Thermocouple Channels: 3
Cooling:
Standard Cooling Method: Air
Number of Cooling Zones: 1
Cooling Tunnel Length: 370 mm
Exit Temperature: 40°C
Number of Cooling Fans: Three 45W
Operating System and User interface:
Windows Compatible PC
On-Screen Thermal Profiling and Parameter Setting
Print Capability
Data Logging & Event Recording
Alarms :Audible, Visual (Light Tower) and On-Screen Display
Dimensions and Physical Characteristics:
Size: L3040 X W1380 X H1445 mm
Net Weight:1220 kg
Utilities:
Power Supply: 220 VAC 3-Phase
Frequency: 60Hz
Operating Power Consumption: 6.5-10 KW
Start-Up Power(Sequential Start-Up Mode*): 16 KW
Current(Sequential Start-Up Mode*): 70A
Total Power (Maximum): 38 KW
Number of Exhaust Vents: 2
Exhaust Opening Size: 8" x 2"
Total Exhaust Venting Volume: 260 CFM
*Sequential Start-Up Mode is the default start-up mode and
limits current draw during start-up.
Miscellaneous:
Hood Opening Mechanism: Automatic Raise and Lower
Related Products
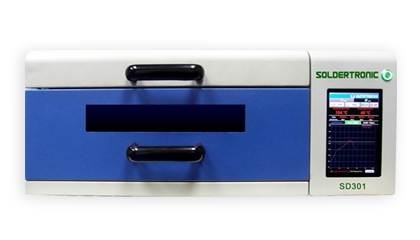
SD301 Bench-top / Batch Reflow Oven
Dynamic Thermal Profile using a Batch Reflow Oven with Android™ Operating System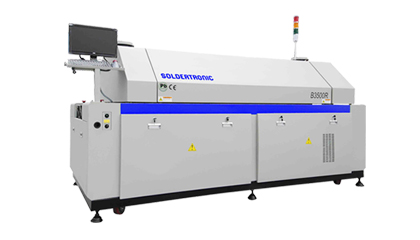
B3500 Convection Reflow Oven
5-Zone Lead-Free Convection Reflow System with Combination Edge-Pin/Mesh-Belt Conveyor and Windows-Based OS!Product Categories
Contact Details
- Sulzbacher Str. 111 92224 Amberg, Germany
- +49 (0) 9621-600 691
- +49 (0) 9621-600 692
- sales@soldertronic.com